In the mid 1970’s a quiet revolution occurred in the climbing community wardrobes throughout New Zealand. For those who can remember it was as though a weight had been removed, we traded our pink and cream Mosgiel woollens for the new brightly coloured, and often striped, revolutionary fibre called polypropylene. Mountaineers returning to New Zealand crammed their bags full of it, while those of us at home collected rationed postal notes to purchase it via international mail order. The conversion was fast and most of us had a couple of sets long before the local manufacturers started offering it. Such was the success of the switch the term “Polypro” became the generic slang for all thermals.
Polypropylene had been around for many years but it wasn’t until Italian researchers discovered how to spin it into yarn that it became relevant for clothing. Originally used as a liner in disposable nappies, it took the very clever visionary Helly Hansen in Norway to recognise the fibre had great potential for thermal underwear. The fabric kept the skin dry and warm by pushing the moisture away. It was ideal for Helly Hansen’s original market renowned for providing functional work wear for North Sea fishermen and ocean oil riggers. Unlike natural fibres, polypropylene kept the skin dry. Continually damp natural fibre, wool and cotton, waterlogged the skin. In sub zero temperatures waterlogged skin became susceptible to frost bite. Polypropylene was so effective the incidence of frost bite on the North Sea became negligible overnight.
Since this time there has been a further advance in fabric technology. Polypropylene hailed from Europe but in the USA most textile manufacturers preferred using polyester yarn. Polypropylene is an incredibly strong yarn but it has a very coarse surface which is easily contaminated. This contamination does not wash free and after a period of time a permanent incrustation of body oils and odours around each fibre builds up, a bit like plague on teeth. There are many old wives’ tales about how you should successfully clean your “Polypros” but unfortunately none of them work as the contamination is permanent. Badly contaminated polypropylene feels oily and in this state the very reason for wearing the fabric, to wick moisture off the skin, no longer works.
Polyester in comparison is a softer, smoother yarn. The smooth surface ensures anything that comes into contact with it during use will wash clean. By engineering the fabric yarns, 2nd generation polyesters from 1985 not only emulated but surpassed polypropylene’s functional properties. In a nutshell, superior performance without the odour build up. Second generation polyesters use a permanent chemical treatment to maximise their moisture transferring and odour free properties. They can also use a mixture of yarn types or a mixture of yarn sizes to alter the surface to assist in this process. The treatment essentially changes the surface of the polyester from hydrophobic, water hating, to hydrophilic, water loving. This changes the surface tension so water and perspiration is transferred outwardly and dries quickly. The same chemical treatment polishes the surface making it even more stain and odour free.
By using a mixture of yarns in the fabric construction (bi-component) the process of wicking, moisture spreading and drying can be further enhanced. These fabrics normally use a faster wicking filament yarn next to the skin and then a softer spun yarn on the outside which first stores then disperses (spreads) the moisture. Spreading is an important drying factor as a droplet of water falling against a t-shirt can dry three times faster if the fabric spreads the water over three times the original surface area. By wicking the moisture through to the outer spun yarn, the filament yarn in contact with the skin dries very quickly. Although the outer surface will feel quite damp and will remain so until the heat from the body eventually dries it off, the inside surface is dry. Dry fibres insulate better than damp ones as moisture raids heat through conduction. It takes very little moisture content to significantly decrease the heat value of an insulation material. A 10% moisture content can halve the insulation ability of a fabric or filling.
Warming up moisture in wet insulation takes a lot of body heat – the wet down sleeping bag effect. Effectively you have to warm up the moisture before the insulation material can bounce heat back to you. In most situations wet insulation is a net raider of body heat not a net provider. Ironically, when you are in a hypothermic situation your body metabolism starts slowing so your ability to warm up wet insulation is also vastly reduced. This can lead to disastrous results very quickly.
Synthetic fibres will only absorb between 1 – 3% of their weight in moisture. If a wet synthetic garment is hung up the water will “drop out” of the fabric very quickly. In the outdoors the final pooling area for dampness is easily removed by flicking dry this area. This is quite different to the natural fibres where moisture absorption rates are well above 15%. Greater absorption leads to longer drying times with very little water “drop out” when the wet garment is hung up to dry.
It is near impossible to construct a laboratory test to simulate all of the variables that one experiences while wearing thermals in the natural environment. For this reason laboratory data is very dangerous as numbers can easily be transformed to tell a myriad of different stories. Be very wary of comparable graphs and marketing claims. In the end it is wearer comfort in the field that is the most important consideration. I was recently asked by a very large marketer of fabric when discussing the performance of moisture management in treated polyester, “Did I have any scientific proof of what I was saying” By asking the question the marketer showed they had very little understanding of thermal insulation in the outdoors. Common sense needs to prevail and I would suggest all outdoor enthusiasts should experiment for themselves with what best suits their requirements for the activities and level of exercise they pursue.
In terms of odour all synthetic fabrics will smell, essentially they will smell as much as their wearer. They are all solid fibres and as such can only store body odour particles on their outside surface. The main difference between polypropylene and treated polyester is polyester washes clean after each wear, polypropylene doesn’t. When you wear polypropylene you immediately get a combined body odour of all the previous wears.
Polypropylene still has its place in the outdoors. As an entry level thermal it is still the best value insulation you can obtain. Treated polyesters are more expensive but in terms of value for money they will not only out-perform but they will also out-wear their well known rivals. Natural fibres do not have wicking, moisture transferring or fast drying properties. Despite all the marketing descriptions these terms firmly belong to the synthetic fabrics. So we now go back to where we started over 30 years ago. Was the passion and zeal to replace our woollen underwear incorrect or unfounded? I would suggest not as the very reasons why we did it then are equally relevant today.
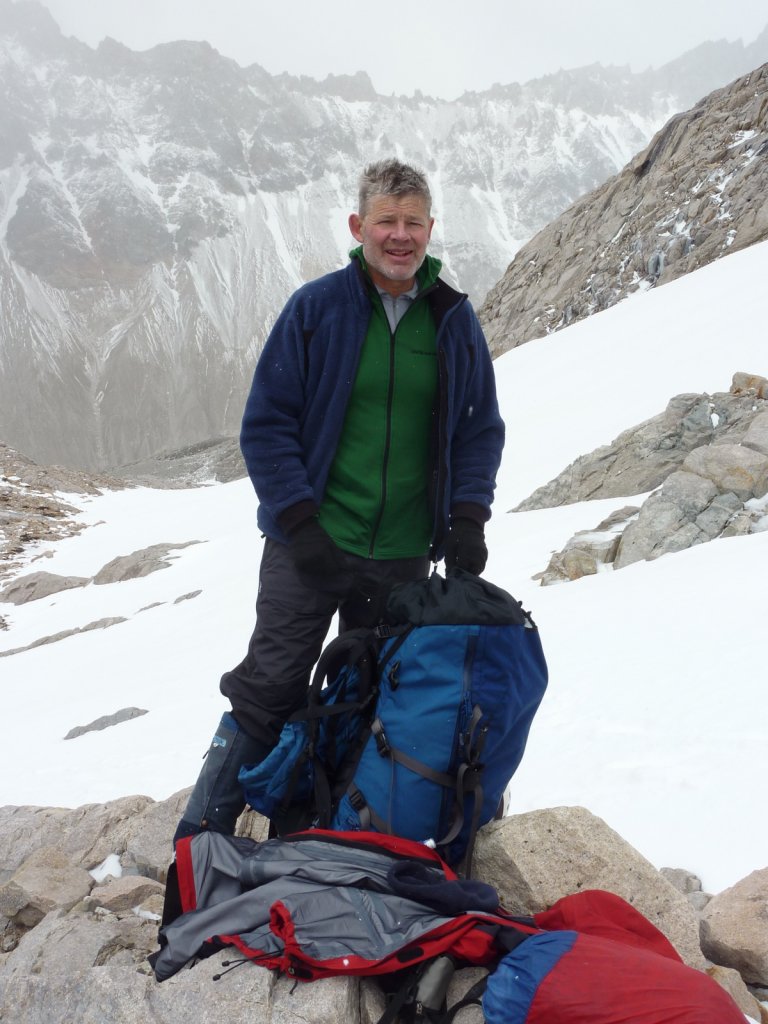
Dave Ellis layering up in Patagonia.
David Ellis established the performance outdoor clothing company Earth Sea Sky in 1990. Prior to this he worked in the then family business Arthur Ellis & Co Ltd for 10 years where he was responsible for expanding the company’s range of Fairydown sleeping bags to include packs, tents and outdoor clothing. Earth Sea Sky manufacture all their clothing in New Zealand and offer a full range of performance synthetic and natural superfine merino next-to-skin thermals. FMC members can receive discounts on ESS clothing.